High Performance Test Systems
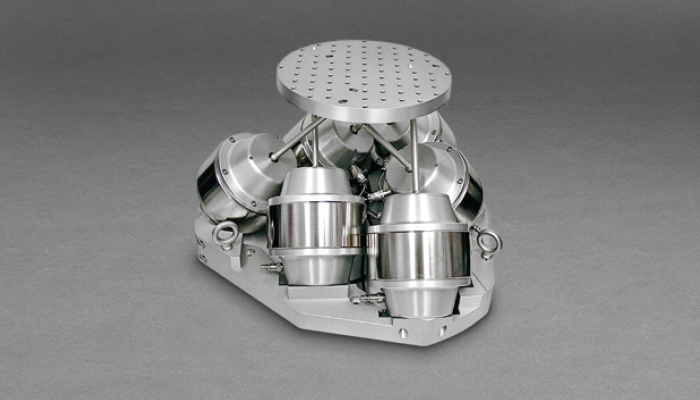
Why Invest In a Test Facility Product?
Our technology excels in the harshest environments, and our test systems make sure yours can too. Our systems replicate the critical aspects of launch or on-orbit operation and are compatible with other test facilities, including vacuum chambers. They help close the gap between the real operating and synthetic environments, thus reducing risk, proving controllability, and avoiding additional partial testing. Traditionally, testing of space flight and other hardware has included thermalvacuum, shock, and vibration tests to screen or test components. Moog offers a wide range of products for more comprehensive testing, simulating loads, vibration, boundary constraints, and other aspects of operational mechanical environments. These test facilities can be used to perform traditional stress tests, but more broadly, they allow our customers to easily assess performance by capturing essential features of operations environments and permit prolonged, comprehensive ground testing and subsystem refinement.
Custom test Systems
Moog will work with you to understand your requirements and rapidly develop a custom system that builds on our established products. Whether you have a long spar incapable of supporting its own weight or an antenna structure, Moog will start with our established test systems and augment them or use different architectures to meet your needs.
Satellite Support Platforms
Our satellite support platforms ease assembly, integration and testing by providing mechanical mounting and decoupling from your facility and its sources of mechanical disturbance. Platforms incorporate vibration isolation and are compatible with atmospheric and thermal-vacuum environments.
- Mechanically decouple satellite from facility
- Compatible with thermal-vac
- Optional latch and release
Gravity Offloaders
Gravity influences structures differently on orbit but those structures must be integrated and validated on the ground. A deployable spacecraft appendage is often mass-optimized for zero gravity performance but unable to support its own weight on Earth. Moog’s no-sag gravity offload systems provide low frequency suspension, with modes as low as 0.1 Hz, enabling you to test and validate fixed and moving space structures before flight.
- Supports weight from above or below
- Payloads up to 15,000 kg
- Optional load leveling
Flight Motion Simulators
Moog offers products that extend the fidelity of hardware-inthe-loop testing, incorporating more realistic aspects of flight including high frequency structural response. With Moog’s six degree of freedom motion bases, you can now evaluate image motion compensation algorithms and position test articles relative to other verification equipment.
- Six-axis motion control
- Hardware-in-the-loop testing
- Real-time interfaces
Launch Vehicle Test Structures
The latest generation of launch vehicles, small satellites and evolving structural concepts drive the need for more sophisticated testing and qualification before flight. Moog designed and built a facility that allows AFRL to test a variety of payload and interstage structures, fairings, and interface cones under multi-axis loading.
- Multi-axis load application
- Structures up to 5 meters
- Test adapters, inter-stages, fairings
Isolation Benches
When a major aerospace company began to develop a new vacuum test facility for large space optics it turned to Moog to provide vibration isolation. Moog delivered a large optical bench, supported by a soft isolation system. With suspension modes in the range of 1 to 2 Hz, the 250-ton bench is mechanically decoupled from the rest of the facility including pumps and other machinery, enabling a high fidelity representation of the space environment.
- Flat optical bench (25 m long) for testing in vacuum
- Isolation system (1.5 Hz) with active leveling for moving payloads
Large Optics Positioners
Moog provides precision positioning systems to support these ground tests. These systems are based on our proven hexapod motion platforms, with resolution measured in micrometers or better. During vacuum chamber operation, they allow softwarecontrolled alignment of test optics and flight components to validate performance of subsystems and complete systems.
- Six-axis motion control systems
- Options for range, speed, precision
- Intuitive user interfaces